Innovative TT-IN-ONE System
Description:
The TT-IN-ONE system revolutionizes automated manufacturing by merging the latest T11 thermoforming machine with precision CNC trimming capabilities. Its advanced gantry system ensures flawless transfer and handling of parts, encapsulating both processes in a single streamlined operation.
Advantages of TT-IN-ONE System
Seamless Integration
Experience unmatched efficiency with the TT-IN-ONE’s seamless integration, where the high-speed gantry system facilitates swift movement between thermoforming and CNC trimming, enhancing throughput.
Optimized Production Flow
Leverage the full potential of your production with the TT-IN-ONE, which provides a continuous flow of operations, reducing the need for manual intervention and maintaining a consistent quality of output.
Space Efficiency & Safety
The TT-IN-ONE boasts a compact design that maximizes workspace efficiency while incorporating features like bellows for protection and a central fan for optimal cooling, ensuring both safety and sustainability in your manufacturing process.
Features
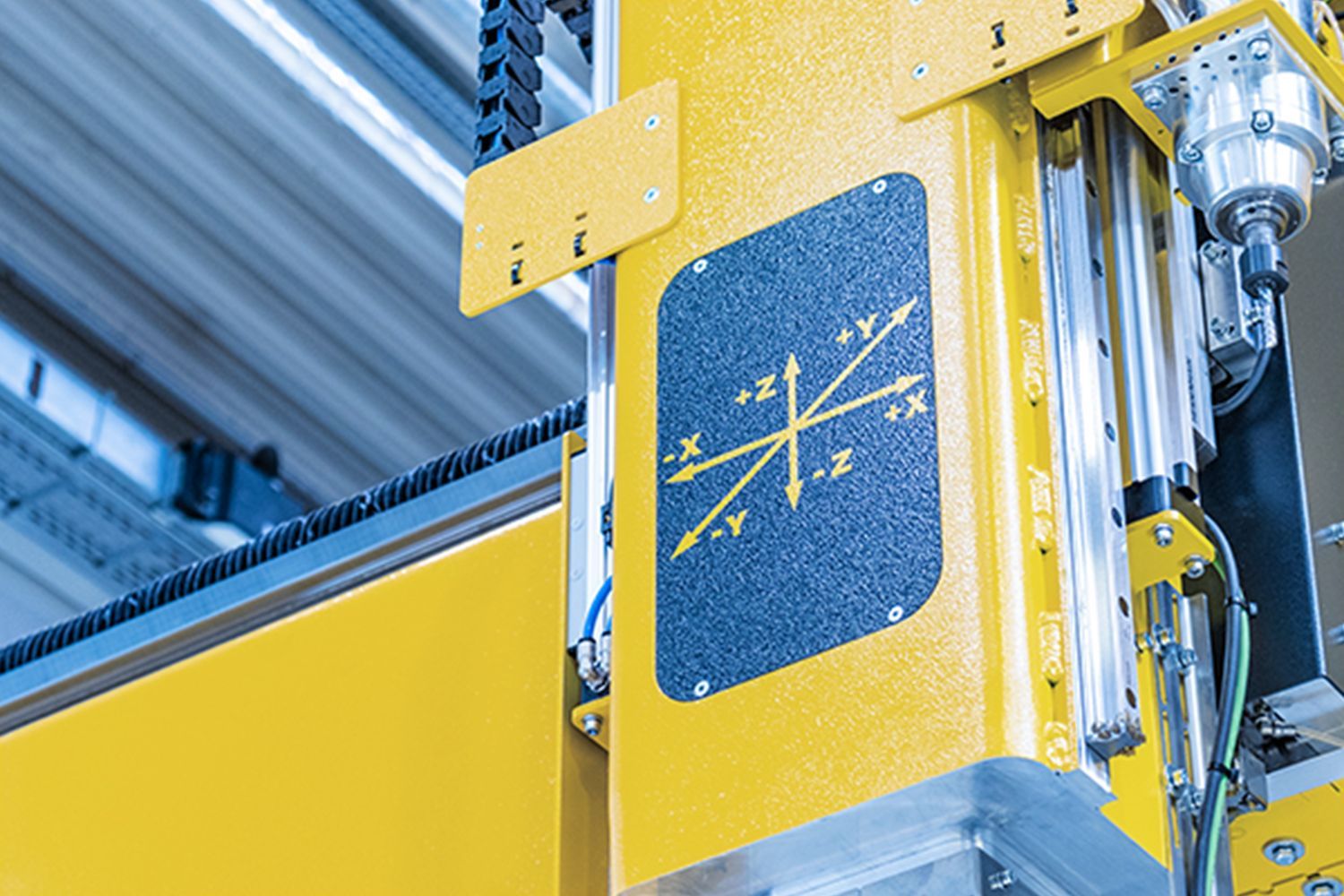
Dynamic Engineering
The unique design of the system offers high stiffness with minimal mass, leading to reduced drive power requirements.
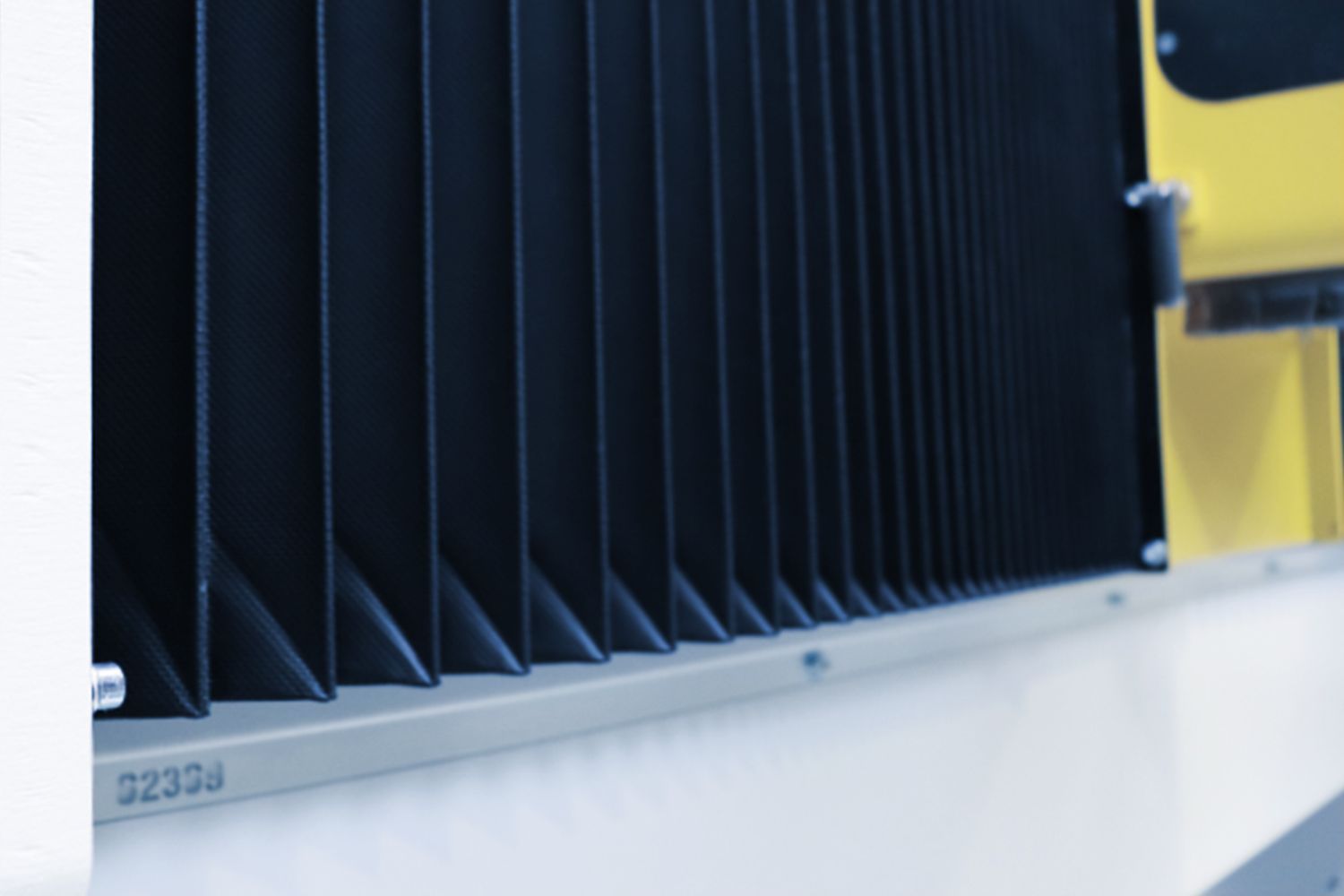
Enhanced Protection
Strategically placed bellows provide effective shielding, safeguarding vital drive components.
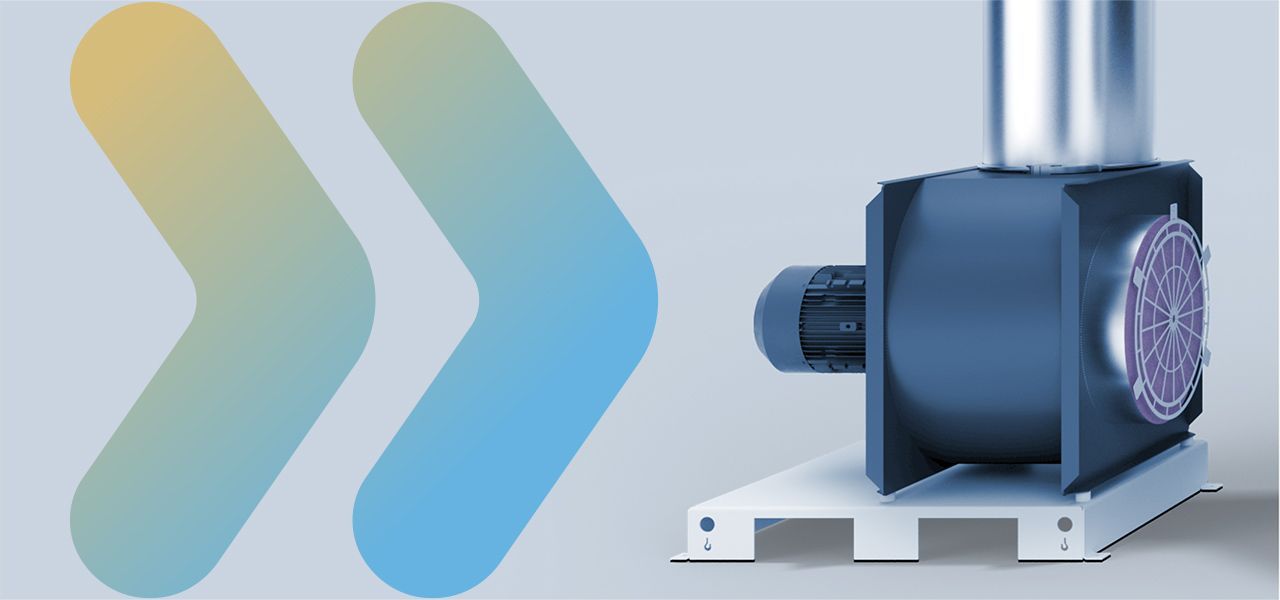
Precision Cooling System
Equipped with a ground-mounted central fan, this system delivers highly efficient cooling, ensuring optimal performance and machine longevity.
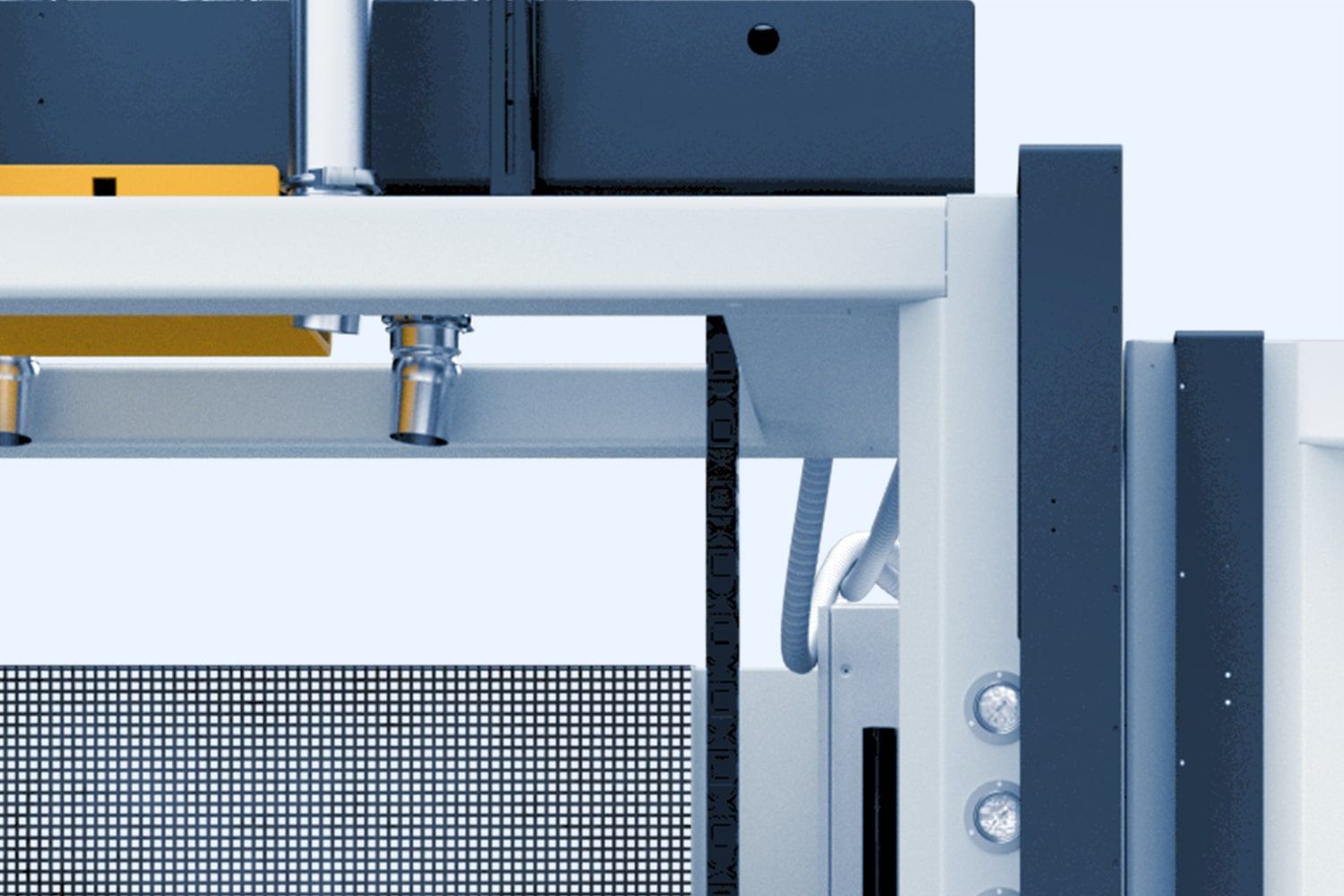
Design Efficiency
The innovative, compact housing of the machine maximizes space utilization, allowing for a range of processing capabilities.
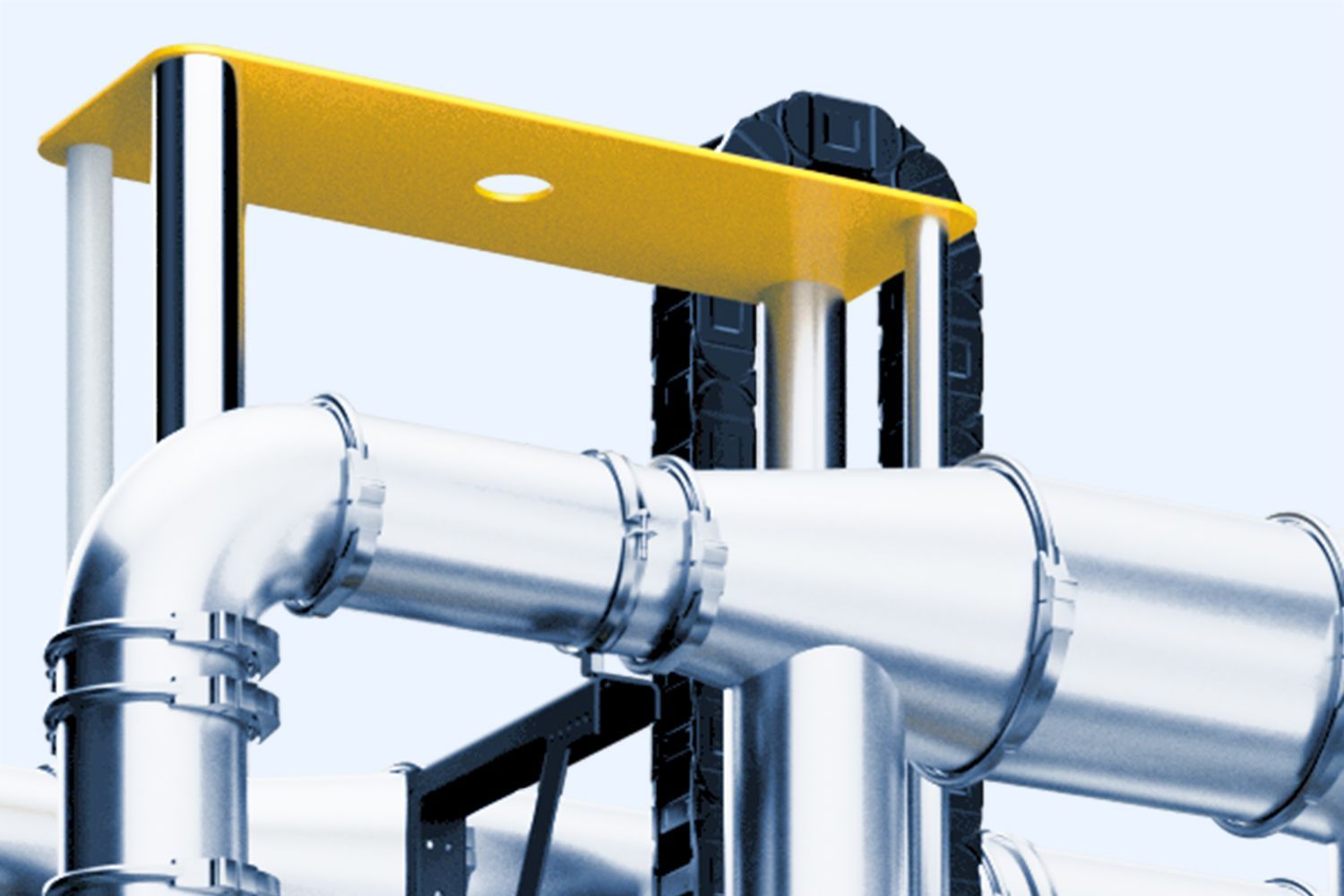
Optimized Piping System
The piping system of the machine ensures peak operational efficiency, reducing energy use and increasing performance.
For more information about the TT-IN-ONE, call us at (860) 605-8643 or complete the form.
Why Choose Us
Over 75 Years of Industry Experience
Long-Term Cost Saving Investment
Lowest Cost Per Part Produced
Optimized Operational Efficiency
Substantial Savings in Energy Consumption
Reduced Material Usage & Lowest Scrap Rate
Highly Customizable Solutions
Professional Service & Support
Frequently Asked Questions
What are the primary benefits of using the TT-IN-ONE system for automated manufacturing?
The TT-IN-ONE system is a groundbreaking automated manufacturing solution by Geiss, LLC, integrating thermoforming and CNC trimming processes. It utilizes a sophisticated gantry system for parts handling, ensuring seamless and efficient movement of parts through each stage of production, from forming to trimming and stacking, all within a single compact system.
How does the TT-IN-ONE system improve the efficiency of production processes?
The system's automation allows for continuous operation with minimal human intervention, accelerating production times and amplifying productivity. Its fast cycle times and coordinated handling and machining processes result in efficient, uninterrupted production, ensuring maximum throughput.
In what ways does the TT-IN-ONE system contribute to cost savings in production?
By automating the manufacturing process, the TT-IN-ONE system significantly reduces the need for manual labor, allowing for continuous operation and eliminating downtime. This consistent performance maximizes the utilization of production capacity, which, in turn, reduces operational expenses and enhances cost-efficiency.
Can you elaborate on the handling and trimming process within the TT-IN-ONE system?
The system employs a CNC-controlled handling gantry that safely transports the thermoformed part to the machining station. Here, parts are precisely clamped and trimmed, with automatic chip extraction ensuring a clean process. Post-machining, another gantry system efficiently stacks the finished parts, ready for the next phase of production.